HSOs must carry out risk assessments before workers do a new task. In addition, updated Health & Safety concerns require risk assessments. Due to proper risk assessments, HSOs can identify potential hazards and workplace risks before they happen.
Hazard controls prevent workplace injuries, illnesses, and incidents. Therefore, HSOs should maintain workers to follow the controls. As a result, an HSO can reduce safety and health risks and provide safe and healthy working environments.
As an HSO, you must train workers to understand hazards and how to control risks. In addition, prepare emergency and non-routine worker protection strategies. Also, evaluate existing controls to see if they are still workable or if other measures are better. For example, new technologies may be safer, more reliable, or cheaper.
An HSO should have the authority to establish safety programmes. In addition, HSOs must ensure contractors have written safety programmes. Then, check if contractors have appropriately implemented them. The programmes should adhere to HSE Standards.
Also, you should focus on work in high and dangerous places, such as ladders and cranes. Monitoring is a part of the Health & Safety Officer Roles. By properly authorising and monitoring, HSOs can eliminate most workplace injuries.
Make Incident Action Plans (IAPs)
The Incident Action Plan (IAP) is a document that details the goals of an incident. In addition, it outlines how the authority will manage the incident during the operational phase. The incident objectives are the basis for the IAP, which details incident organisation, work assignments, resources, and safety. Therefore, creating a proper IAP is part of the Health & Safety Officer Roles. For example, an IAP in a healthcare organisation (HCO) may include the following.
• Scenario
• The intent of the HCO
• The aims of the HCO
• Strategies for HCO
• Allotting HCO Resources
• Updates on HCO events
• Administration/Finance
• Transmitted Message
• Projection of the incident
Investigation of Incident-Area Accidents
To gather reliable information, HSOs must investigate a work-related accident or injury immediately. Accidents are unplanned and undesirable events. However, all accidents will not necessarily end in injury. An incident is an unwanted event that may cause bodily harm or other damage.
As the best practice, HSOs should examine all accidents and incidents regardless of their severity. So, you should include no-damage situations or near-misses. All in all, accident investigations can identify safety concerns and training needs to lower injury rates.
Toolbox meetings are brief, straightforward, and uncomplicated safety talks before work. Besides, they are referred to as safety briefings, pre-starts, or safety talks. It’s a discussion among employees that lasts 5-10 minutes regarding their Health & Safety hazards.
A good toolbox meeting encourages workers to share knowledge and best practices for safety. As a result, HSOs can foster a culture of safety in the workplace.
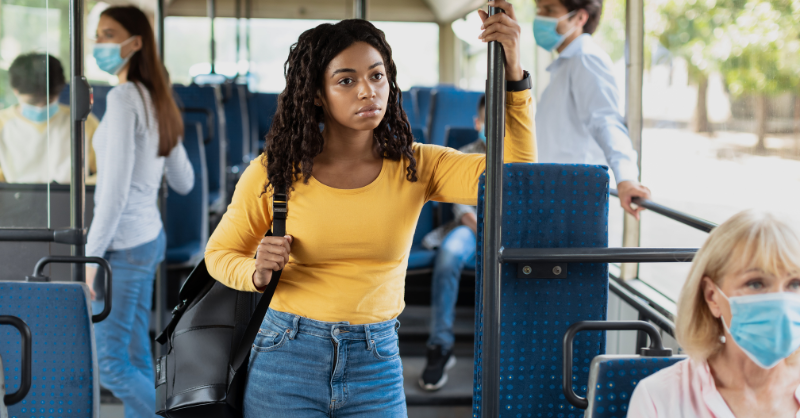
HSOs help a business build safety councils. Upper and lower management, workers, and HSOs form safety councils. A project safety council is a specific council for a particular work. A new project may require a panel of experts. In contrast, a new project might not need a new council, and the old council is appropriate for the project.
By building good safety councils, HSOs pave the way for best practices in health & safety.
Approval of Subcontractors’ Safety Plans
An HSO is responsible for reviewing the subcontractors’ safety plans and finally approving them. Unfortunately, hazards can occur due to unchecked and faulty procedures. So, properly supporting the safety plans is an essential duty of the HSOs.
Delivering Injury Logs and Reports to Government Authorities
The HSE demands you deliver injury logs and reports to government authorities. It’s a mandatory duty of you as an HSO. According to the Reporting of Injuries, Diseases, and Dangerous Occurrences Regulations (RIDDOR), employers and anyone else in charge of the property are required to report workplace accidents that “result in certain serious injuries to employees or render them unable to work for more than seven days straight”.
In addition, HSOs will hand over injury logs to the appropriate enforcement authority and keep maintaining records of these incidents.
Routine Check of Tools and Equipment for Safety
A workplace may contain a lot of electrical equipment. In addition, a business may be located in a hazardous area. Safety issues are different for each workplace. Therefore, you must understand the nature of the premises first.
In addition, you must decide what is dangerous in what workplace. For example, a box made of stiff paper can cause an accident if workers carry them on a slippery floor. In contrast, toxic chemicals contained correctly in steel drums won’t cause harm to the workers.
As the manufacturer recommends risk assessment, HSOs must inspect equipment regularly. For example, manufacturers may recommend daily checkups. A routine check will reduce dangers from blockages, leaks, and malfunctions.
As an HSO, you must maintain guards, alarms, safety cages, and warning signs surrounding the equipment. In addition, check the surroundings around heat-producing equipment routinely. For example, ensure clear floors and enough ventilation. Also, maintain fire detectors and remove flammable objects.
Moreover, laws demand inspections of some equipment. Such as, gas appliances, lifting equipment, pressure systems, and power presses require expert reviews. Also, keep records of your checks, including findings and repairs.
Promoting Workplace Safety
You can promote workplace safety by rewarding workers who maintain the highest safety. In addition, you can use more labels and signs due to their ability to rapidly and cheaply convey critical information. Finally, you can use visuals to explain hazards and procedures.
Workplace clutter can cause trouble. Safely stack boxes and swiftly clear spills. In addition, check for tangled cords, untidy flooring, and cluttered tools regularly. In addition, provide stretch breaks if possible. Stretch breaks boost ergonomics and staff wellness. Therefore, encourage five minutes of stretching to relieve muscle tension and loosens joints, decreasing repetitive motion injuries.
Workers can recognise and report hazards immediately. Therefore, communicate with them to acknowledge safety issues.
Practising Emergency Response Drills
Prompt and effective emergency response could help to calm the situation and control its effects. It would be best if you practised emergency response drills. It’ll help workers to be competent and well-trained. In addition, practice frequently and realistically. Introduce clearly defined, recorded, and practised plans, actions, and duties.
Also, write an emergency plan if a significant workplace incident could jeopardise the general public, first responders, emergency services, and coordinators.
HSOs must provide necessary safety guidance under the HSE Safety Guidelines. As an HSO, you are responsible for spreading safety awareness among workers. Therefore, you should hand them hard and digital copies of safety guidelines. Having copies will help them reassure safety in the workplace.
Updated Policies and Measures According to Law
Guidelines, policies, legislation, and measures are all ever-evolving things. Authorities or governments can change them due to the constant occurrence or invention of new hazards or new technology. As a result, old policies won’t cover all the safety issues. You must update policies and measures continuously.
Inspection of Workers for Non-conformity
You have to search for faults in the workplace thoroughly. However, sometimes managers or workers show resistance to following guidelines. In that case, you have to clarify the rules again to them. In addition, make them understand the consequences of not following your Health & Safety Officer Roles. Finally, if they adhere to their obstinate position, take necessary action and report to the upper management.
Managing Installations, Maintenance, and Waste Disposal
Businesses conveniently buy new equipment or repair old ones. As an HSO, you must adequately manage the installation of new equipment. Sometimes, old ones might not work due to insufficient maintenance. Such occurrences produce a loss of profit for the company and create safety issues for the workers. Therefore, you must ensure proper care of all the equipment.
Last but not least, don’t forget to supervise the waste disposal. According to a study, more than 80% of waste disposal injuries happen because of improper disposal. Also, medical waste disposal injuries may cause workers to contract HIV, hepatitis B, and hepatitis C.
HSOs must supervise the Permit-to-Work (PTW) systems. PTW helps manage work activities, including non-routine activity, and is a crucial component of work safety. It’s a formal authorisation system to manage particular work and guarantee the safe execution of work on-site.
Being an HSO requires you to be a part of the emergency response team. If an emergency occurs in the workplace, you have to take proper steps. Emergency response should be flexible but follow a set of principles.
• Anticipation
• Preparedness
• Subsidiarity
• Direction
• Information
• Integration
• Co-operation
• Continuity
For more detailed information, take our Emergency Planning and Management Course.
Informing the Management of Training Needs
Workers need Health & Safety training regularly. Especially, a new worker who is not familiar with workplace hazards needs training as soon as possible. HSOs are responsible to train or hire professionals to train the workers. As an HSO, you must inform the higher management when training becomes necessary.
Storing and Labelling Hazardous Substances
As an HSP, you have a legal obligation to make sure that hazardous chemicals are properly labelled whenever workers use, store, or handle them. Correctly labelled hazardous chemicals are simple to spot. And they effectively warn the workers of potential health and physical risks.
However, if a chemical label comes off a container of dangerous chemicals, you need to have protocols in place. For example, you must ensure employees don’t spill fuel or cleaning supplies while decanting them in containers.